We calculate the CO2 emission of your Primo profile
Did you know that it's now possible to get a real-time carbon footprint insight into any moving bed biofilm reactor (MBBR) – sequencing batch reactor (SBR) project you have? We can extract the CO2 emission figures by entering the data from the plastic profile we produce for your product into a sophisticated CO2 calculator.
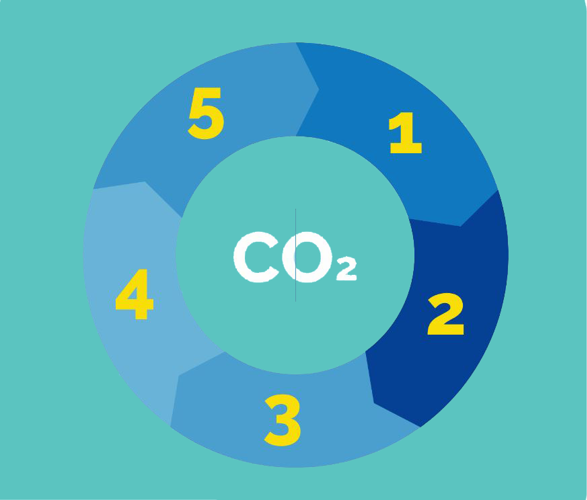
After years of research and testing, 2024 is the year we calculate the carbon footprint of the profile we design and tailor to each customer's solution. We have partnered with experts in the field to provide the data and documentation that will enable us to calculate the cradle-to-gate CO2 emissions and reductions of every single plastic profile that leaves one of our manufacturing facilities.
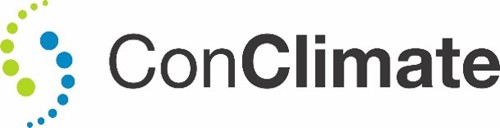
Together we make the difference
Measuring the carbon footprint is a key factor in the water treatment industry. Primo can support your development project and your solution as a whole: In the field of plastic extrusion for water treatment profiles, the use of future-proof technologies is paramount. Plastics are emerging as a prime candidate for sustainability due to their inherent qualities: durability, non-reactivity, light weight and minimal maintenance requirements. We should always address unique properties like these when we co-create new solutions.
How to reduce CO2 emissions
When it comes to the plastic profile designed for your product there are several ways to reduce your carbon footprint, directly or indirectly. Some examples:
- Designing profiles with less material and reducing their weight
- Choosing the right type of plastic raw material ensures the longest possible service life
- Switching to post-consumer recycled plastics or blends of recycled and conventional plastics.
- Switching from fossil-based materials to non-fossil (bio-based) materials.
Throughout our supply chain, we are reducing our energy consumption at manufacturing sites and improving production technologies, which contributes to manufacturing more sustainable profiles.

Primo’s FUTURE FIT commitments to sustainability
Here at Primo, we've embarked on a journey towards sustainability by setting specific targets across the Group. Our overall goal is to help our customers reduce their CO2 emissions. As part of our FUTURE FIT initiative, we are constantly exploring new material combinations, including recycled plastics, bio-based alternatives, recyclable variants and innovative material blends.
The ultimate goal? To improve the sustainability performance of your end product through increased energy efficiency, extended durability, reduced maintenance, reduced weight and more.
Our ambition is not only to be FUTURE FIT ourselves, but also to help you and your customers reduce your carbon footprint.
About wastewater systems:
Wastewater systems play a crucial role in maintaining clean water supplies, protecting public health, and safeguarding the environment for current and future generations. MBBR system installations filter water by inserting biomedia into the water tank.
Small polyethylene or polypropylene carriers support the growth of bacteria, which biodegrades the waste in the water, resulting in a clean effluent. Biofilm carriers are very effective cleaners of wastewater and sewage water. They are used worldwide in municipal wastewater systems and for cleaning in a wide range of industries. We’re talking about a fantastic environmental-friendly solution for providing clean water, which absolutely calls for a responsible - and as green as possible - supply chain.
About Primo
Headquartered in Copenhagen, Denmark, Primo A/S operates 12 sales and production sites across Europe, China and the USA. Founded in 1959 by the Grunnet family, Primo specializes in custom-designed plastic profile solutions. The company employs around 1000 people and reported a turnover of 180 million EUR as of December 31, 2024.