CO2-emission calculation at Primo
C02-documentation provides your company with a measure of your climate footprint and can identify emissions hotspots across your value chain. Companies all over the world measure and report their C02 to stakeholders and use the findings to inform about their sustainability actions.
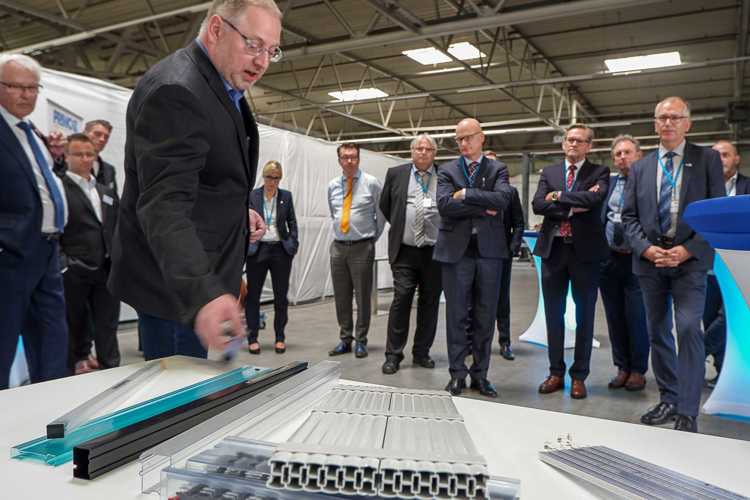
Plastic is a part of the solution. This has been the mantra at Primo for some time now. An essential part of this is to deliver on customers growing demand for CO2 life cycle accounting. This is important in a range of sectors, for instance, in the construction sector, where new buildings are planned and designed under certain limits for total lifetime CO2-emissions. The same is seen in the auto industry. Here, carmakers are interested in understanding the total emission of producing a car, both for CSR-reasons and as an increasingly important part of their marketing.
We can now share CO2-data with customers
At Primo, we have a good understanding of our production-related CO2-footprint. This knowledge can be shared with customers who wish to calculate, document, and present a complete overview of their products' total CO2-footprint. As a specialist in our products, we also try to reduce unnecessary CO2 in transportation, and we offer this experience to our customers.
The area is in its infancy, but we can already give our customers a rough but pretty confident idea about what kind of CO2 footprint is associated with profiles from Primo. There are two significant sources of CO2 emissions when producing polymer profiles: Energy to produce profiles at our facilities, and the emissions related to the raw material. - We are in the fortunate situation that we have these data.
A simple CO2-calculation
Primo's raw material (virgin material) suppliers guarantees that their products have an impact of 1,62 to 1,99 kg CO2 pr. Kg. PVC. The energy consumption to produce profiles at Primo's factories can be divided into the number of kgs. Produced profiles. The result from the factory in Berlin is 1 Kg. PVC profile = 0,750 – 0,800 kWh.
1kWh energy means 474 gr, so for extrusion, you must add 0,36 – 0,38 kg CO2. So:
1,62 - 1,99 kg CO2 eq/kg raw material PVC + 0,36 – 0,38 kg for extrusion = 1,98 – 2,37 Kg CO2
One could argue that this number is just a part of the total, since there are many other sources of CO2-emissions. For instance, the employee's transportation to and from work, transportation of the profiles and raw material, - and even the construction of the extruders and the entire production facility. The list could go on, but what is important here is that we are now able to document the energy consumption and calculate figures that are comparable with other products and types of suppliers.
CO2-footprint advantages of polymer in comparison with other materials
Polymer/plastic is lightweight, which reduces transport-related CO2
Production of polymer profiles generally has a low CO2-footprint compared to energy-consuming production of steel and wood profiles
Polymer is far more C02-friendly when it comes to recycling than any other materials.
Recycling matters in the CO2-calculation
By replacing one ton of virgin plastic with recycled material, the industry can save between 1.1 – 3.0 ton/CO2, according to the Sustainable Plastics and Transition Pathway model (STEP) and The New Plastic Economy by the Ellen MacArthur Foundation.
About Primo
Headquartered in Copenhagen, the Danish group has sales and production activities at 11 locations in Europe and China. The group currently has 980 employees and a turnover of 205 million EUR (per 31.12.2022). The company was founded and owned by the Grunnet family and, since its beginning in 1959, has specialised in designing and producing customer-specific profile solutions in plastic.